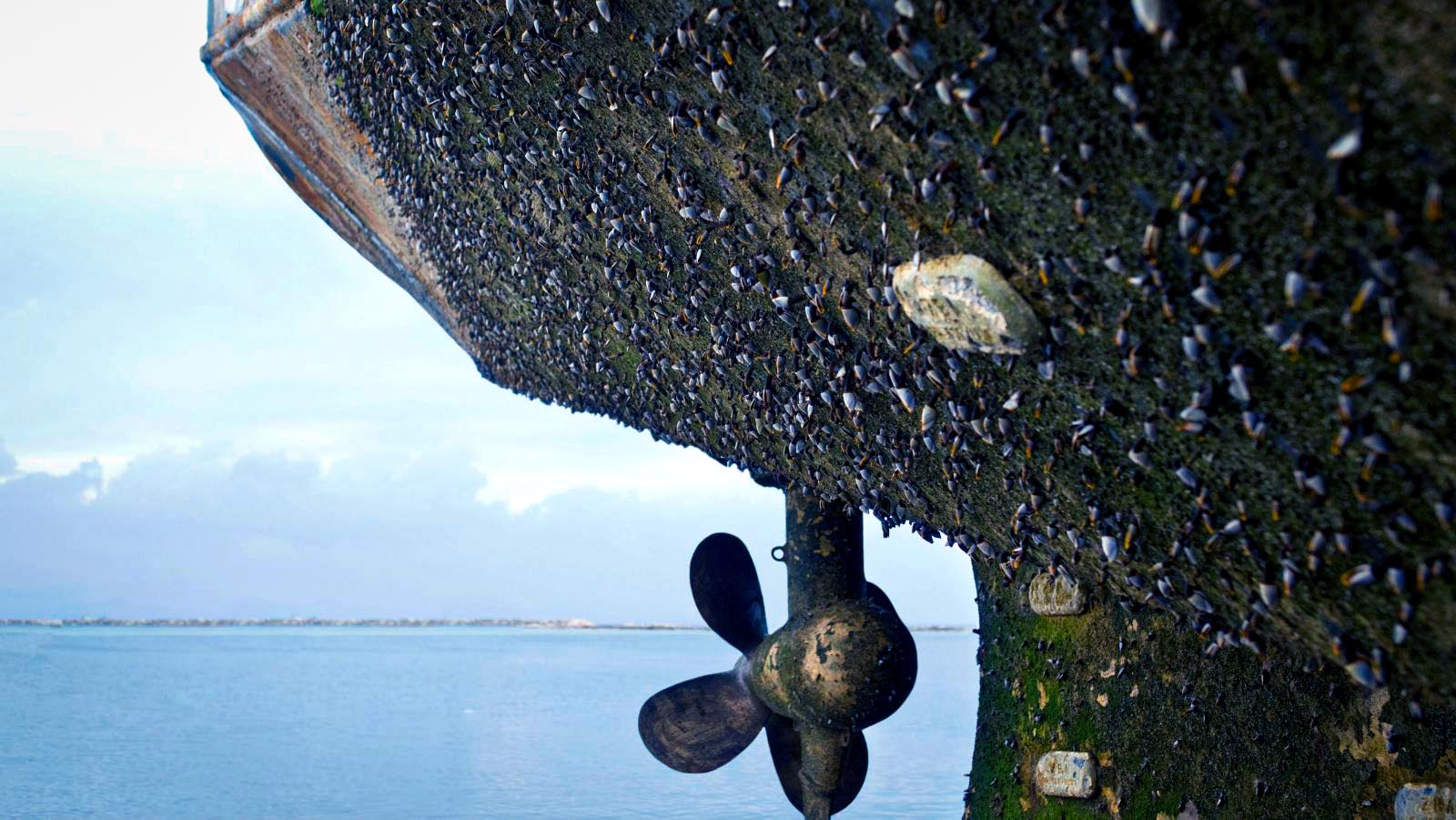
November 21, 2023
Foul Hulls Lead To Foul Performance
After a voyage, the bottom of a ship usually has a layer of marine microorganism colony attached to its hull. This layer of prolific build up is referred to as ‘fouling’, caused by barnacles or tubeworms, among other organisms. The build-up causes turbulence, cavitation and noise, frequently affecting the performance of sonars, speed logs and other hull mounted sensors. In spite of the modern mechanisms in place to protect the ship against similar outgrowth, this layer can be 500 millimeters in thickness and sometimes even more.
Due to fouling, the speed loss is 30% of the rated capacity, the fuel consumption increases along with the inefficiency in speed. The regular underwater cleaning of the ship makes it possible to restore the initial speed by 95-98% and respectively to decrease the fuel oil costs which, as a rule, account for almost half of the operating costs.
The purpose of underwater hull cleaning is to remove biological roughness or fouling. Further, the cleaning and polishing of the propellers lead to the decrease in cavitation which destroys the surface of propellers. Propeller cleaning improves the ship efficiency which is why the ship’s hull underwater cleaning, cleaning of the sea valves gratings and other structural members are so demanded today all over the world.
Dry Docking hull cleaning
The underwater cleaning of the hull, propeller, sea valve gratings and other structural components subjected to fouling do not require docking today. Throughout the years Master Divers have invested in the development of state of the art underwater hull cleaning equipment which provide ships the necessary services to clean hulls underwater and avoid drydocking.
The uniquely designed underwater hull cleaning units provides the necessary durability requirements demanded by the harsh underwater environment. All systems are carefully constructed so that no damage will occur to those hull coatings which are suitable for underwater cleaning, while still completely removing all types of fouling. This restores a vessel’s performance to as close to its optimum condition as possible and offers shipowners considerable savings in fuel.
The scheduled underwater cleaning of the hull is economically advantageous during the inter-docking period, for example, such measures can save up to 900 t fuel oil/year for a shipowner having a tanker of 50 t displacement.
Hull Cleaning
There are a number of options for hull cleaning; the most common is the use of diver-operated machines fitted with rotating brushes. With this methodology, the least aggressive cleaning brush is used that will effectively remove the fouling to avoid excessive anti-foul paint wear.
The frequency of underwater hull cleaning is dependent on the performance of the anti-foul paint. The performance of such paints and the fouling rate can be affected by many factors including time in operation, season of the year, and the geographical region of vessel operations.
An emerging hull cleaning technology is the Hull Surface Treatment system, which uses a containment device attached to the hull that pumps out hot salt water which is said to kill the foul-creating marine organisms; these then wash off under normal operating conditions.
Even with the emerging techniques, the tested and proven old methods of hull cleaning are used sometimes when the degree of fouling on the hull is extreme.
Mechanical cleaning by means of the hydraulic metals is indispensable in the case of heavy fouling as well as when the ship should be cleaned very quickly during the ship’s stay at anchor or in port. This is done through underwater cleaning by means of a machine driven by hydraulic pressure and is based on the action of the rotating brush driven by the hydraulic motor.
Coaxial hose supplies the hydraulic liquid from the pump station arranged above water. Special design of the brush makes it possible to fit tightly like sticking to the surface being cleaned. Brushcarts-brushes can clean both the horizontal and vertical surfaces and can also remove practically all existing types of fouling (shell molluscs, algae and others). The hull main coating is not subjected to risk of damages in spite of rather powerful effect onto the surface of the machine. This is owing to the special materials of which the brushes are made. The level of brush hardness selected so that the varnish-and-paint coating on the hull is not damaged.
The next method is hydrodynamic cavitation, which removes the fouling from the ship’s surface maintaining its varnish-and-paint coating. This procedure is carried out where it is impossible to clean by the mechanical method. The hydrodynamic cavitation is effective where the cleaning of the vent distribution ducts, sea chest gratings, sea chests, valves is required. As a simple example of cavitation; take normal boiling water, when the steam pressure is equalized with the environment pressure, bubbles form and flow to the zone of higher pressure. With this motion the bubbles seem to slam creating a strong shock wave. The principle of operation of the plant for the hydro-cavitation cleaning is similar to that of the strength of a high impact jet which delivers under certain pressure. Steam-gas bubbles, coming to the surface which should be cleaned, collapses. This cleans the hull and other structures against rust and fouling. The underwater cleaning of hull by means of the hydro-cavitation plant removes all without any exceptional types of fouling, rust, paint; and another advantage of it is that hydro-cavitation equipment is eco friendly.