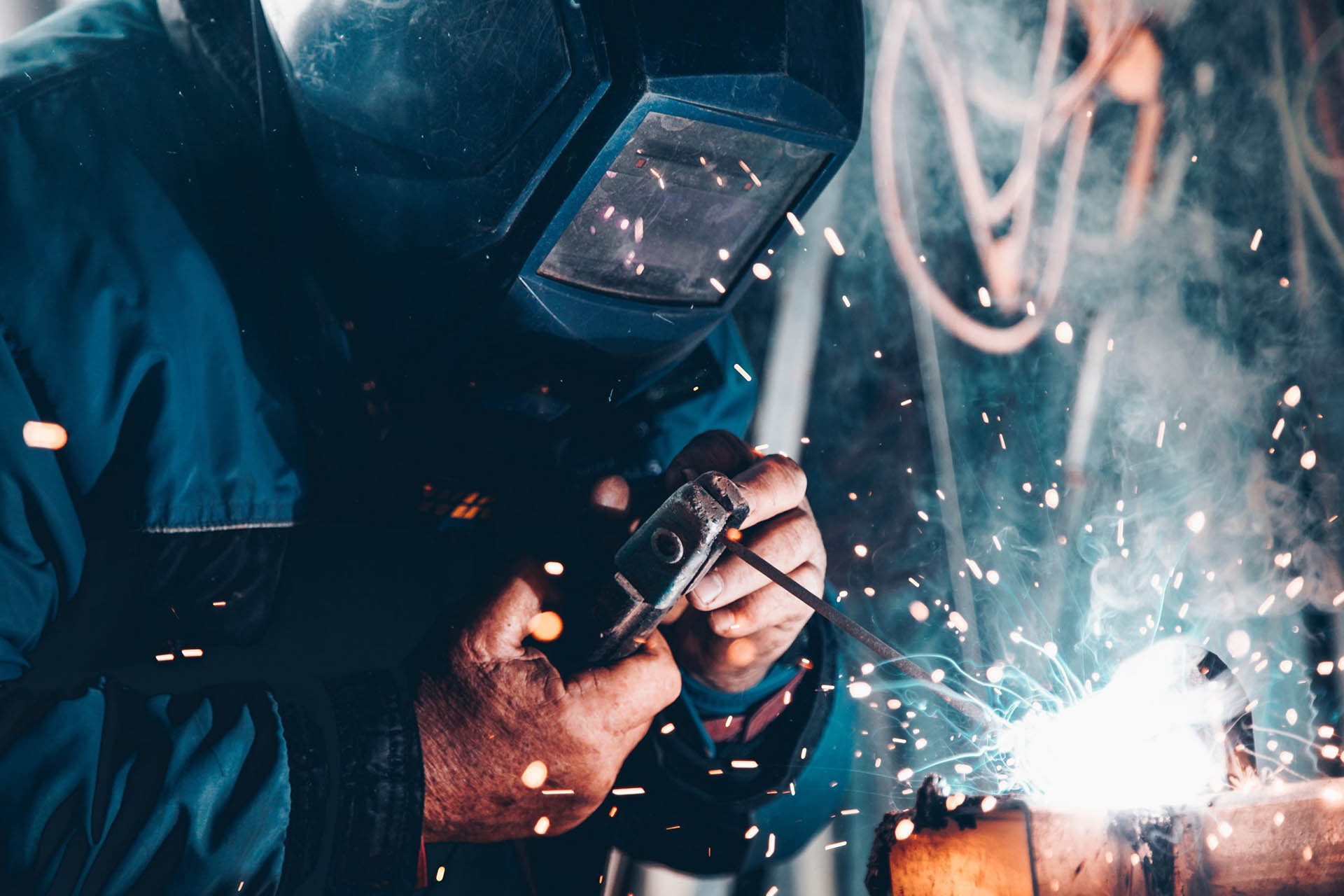
November 20, 2023
Welding Problems That Need Solving
Welding is one of the most critical operations in ship construction and usually the main strategy in fixing flawed ship structures. When welds fail, often the whole structure fails.
When welding takes place wet in the water itself it’s referred to as “underwater welding”and when it’s in a dry environment, inside a specially constructed positive pressure enclosure it is referred to as “hyperbaric welding”.
Consistent weld quality is achieved in practice, through ship classification society regulations, welding procedure qualifications, welder certification, weld monitoring and control. However, no matter how rigorous quality control is, sometimes things go wrong.
There are a number of methods that help in remedying the effects of poor quality welding.
Fitness for Service Assessment
Repairing a flaw might not be always necessary for ensuring structural integrity; e.g. a weld containing a small flaw could still be fit for service.
This is where a fitness-for-service assessment is important. Most regulations specify maximum tolerable flaw sizes based on good craftsmanship; i.e. what can reasonably be expected within normal working practices. However, failing to achieve these requirements does not necessarily mean that the structure is at risk of failure because the requirements tend to be arbitrary.
A fitness for service (FFS) assessment (also called engineering critical assessment or ECA) is an analysis, based on fracture mechanics principles, of whether or not a given flaw is safe from brittle fracture, fatigue or plastic collapse under specified loading conditions.
The FFS assessment process is issued in a number of national standards. The results help in deciding if a flaw that is tolerable could be used in service, or when an unacceptable flaw needs to be removed or repaired. Mostly used in assessing flaws such as fatigue cracks that have grown during service, the life extension of a vessel’s service can also be justified using this assessment.
The concept is widely accepted by a range of engineering industries such as oil and gas, and power generation. However it is not accepted by certain classification societies, despite its long track record in preventing unnecessary repairs, cost and delay while ensuring safety in service.
Repair Welding
Repairs to welds are expensive; up to 10 times the cost of getting it right the first time. Most classification societies, and the IACS shipbuilding repair quality standard [1999], do not allow any weld cracks to be left unrepaired irrespective of size.
Flaw removal methods include grinding or machining a smooth profiled groove, and then inspection to ensure the flaw has been entirely removed. However, before the weld flaw is fixed, it is important to know why the defects occurred, so that they can be avoided in the repair weld. Many problems are caused by either the welder, or from issues with the fit up. Therefore it might be necessary to re-train and re-certify the welder, and/or improve the fit-up of the joint. Repair welding must be done using the same quality controls as the original welding (i.e. approved WPS, qualified welder and certified materials), but if after following the welding parameters of the original WPS has resulted in defects, the WPS might need to be revised.
There is usually a limit to the number of times it is permitted to re-weld, for example DNV allows only two cycles of repair. The repair weld will usually be inspected using the same NDT methods as originally applied.
Fatigue improvement testing
Fatigue cracking during service is a critical issue which arises with regards to the structural integrity of welding in ships. Fatigue failures usually tend to start when cross sections are changed; machined grooves, bolt holes, sharp flaws or at welds. The sharper the notch, the higher the stress concentration, which leads to fatigue life having a shorter lifespan.
The risk of fatigue can be reduced in structures by either reducing the loading on the structure, or by reducing the local stress concentrations by improved design. Misalignment and distortion of welded joints will lead to reducing the fatigue life span as it increases the stress applied on the joints further.
To improve the fatigue of the structure, intrusions at the weld toe joints should be removed to achieve a smooth transition between weld metal and parent plate. Different welded joint configurations are given a classification according to their fatigue performance [BSI 1993]. For fillet welds it is possible to dress the weld toes by grinding away material along the weld toe to remove the toe intrusion while maintaining a smooth weld profile. The toes may be dressed by the careful use of a disc grinder, making sure any machining marks are parallel to the axis of the main stress, to avoid forming initiation sites for further fatigue.
By testing for flaws, before replacing or removing welds, costs can be curtailed. Identifying the core structural issues in the build will lead to understanding the competency of the welders, WPS used and the best practices followed by the marine operations firm hired. Therefore, measures can be taken for the recertification of welders, updating the WPS or assessing the need to change the marine engineering firm to a better quality service provider.